Defying Extremes: the Power of Shock SRS Testing
Shock SRS (Shock Response Spectrum) testing is commonly used in various industries and applications to assess the impact resistance and ensure the structural reliability of products and systems. Cebi Testing Services acquired a new module to extend its vibration offer and respond to needs from the aerospace, automotive or construction industries.
How does the SRS module work?
The new module analyzes the reaction of an object to a shock. The vibration bench generates an impulse of defined frequency and amplitude. The client then analyzes the object's response to this impulse. This new module makes it possible to use the Shock SRS category as a supplementary module. It simulates a short-duration transient shock, with high amplitude.
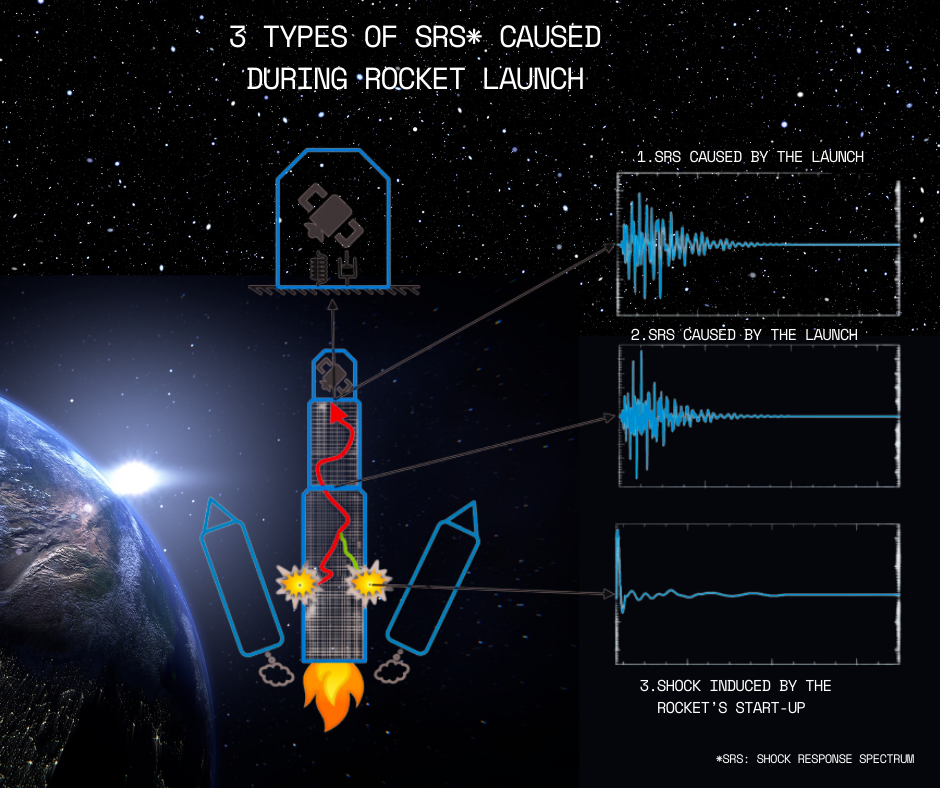
A customer came to see us to make sure that if the optical fiber came back to earth, the optical fiber would arrive on earth intact and test whether the optical fiber would withstand the drop. Another one, wanted to assess the resistance of a 3D printing machine during launch and landing on the ISS (International Space Station)*” - Sebastiano Rizzi, Cebi Testing Service Engineer
Cebi Testing Services has simulated rocket take-off and landing for the aerospace industry. These systems are used by NASA, and are one of the prerequisites for authorization to send objects into space. Components intended for space travel undergo meticulous testing to guarantee their structural integrity under extreme conditions of launch and re-entry into the Earth's atmosphere. This module enabled Cebi Testing Services to check the integrity of the structure, if the part responds correctly to the impulses.
What is the advantage?
The advantage of SRS Sine & Burst Testing benches is that the test can be carried out on a classical vibration bench without the need for a specific shock machine while retaining the same temporal characteristics.
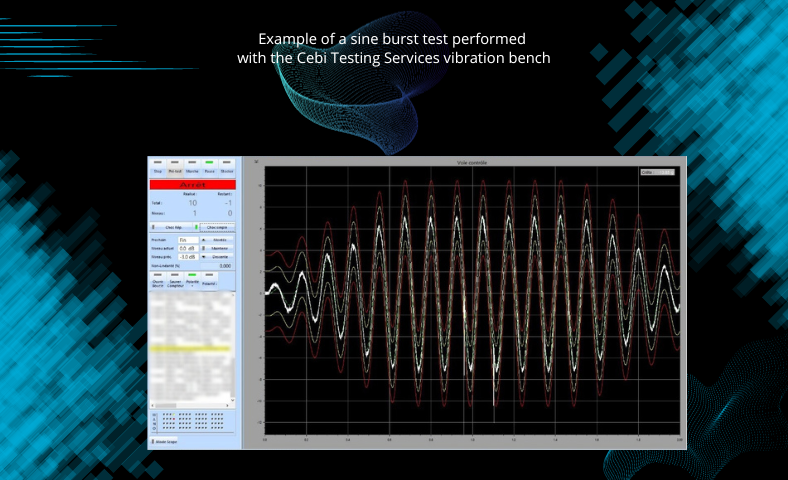
Most laboratories use sine tests, which do not represent completely the true phenomenon. They are different from shock effects, which are less continuous and therefore closer to reality. Shock severity is not present in sine effects. With this module, tests are performed at low frequency and high acceleration.
Beyond Space...
Shock SRS testing is essential in many industries to ensure the safety, reliability, and performance of products and systems under real-world conditions and to meet regulatory and quality standards.This innovation has revolutionized the assessment of impact resistance, providing a closer representation of real-world scenarios compared to conventional sine tests.
It can be used by all companies to test their components against transportation conditions like rough roads, to minimize the risk of damage during transit. Manufacturers strive to guarantee that parts endure transportation stresses, remain intact, and maintain their intended functionality upon arrival at their destination.
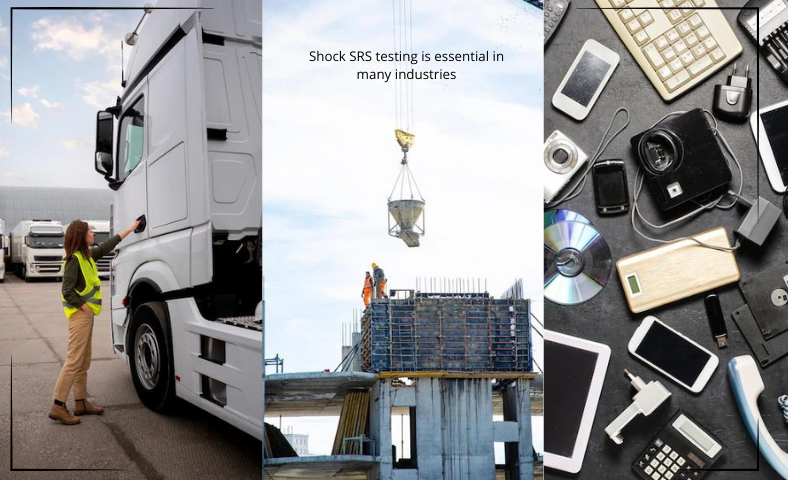
The Automotive Industry leverages Shock SRS testing to evaluate the performance of automotive components like airbags, seat belts, and suspension systems during collision scenarios to enhance passenger safety.
Construction companies can use Shock SRS testing to assess building structures and bridges for their resistance to seismic activity and other dynamic forces.
Conclusion
Its ability to replicate real-world shock scenarios and assess the response of components has positioned Shock SRS testing as a crucial tool in product qualification and reliability assessment, offering the assurance of durability even in the most extreme conditions.
More information
Download the related fact sheet: Vibration Testing.pdf (cebi.com)
Contact us Now: Sebastiano Rizzi
Cebi Testing Services
Phone: +352 33 20 71 921
testing.lu@cebi.com
Visit our Webpage: Cebi Testing Services - Your Innovation Partner | CEBI