Cebi’s Breakthrough in Latching Systems: how to Make the Impossible, Possible.
Cebi’s Breakthrough in Latching Systems: how to make the impossible possible.
Today, Cebi produces over 8 million latches per year for leading OEMs, including hood and tailgate latches. By leveraging the team’s expertise in fine blanking and advanced kinematics, Cebi was a key player in the latches’ revolution. While until the mid-90s, locks were mainly mechanical, Cebi succeeded in designing automated solutions, reliable in all usage conditions.
Let’s see how the perfect combination between young, creative engineers and more experienced ones made the impossible possible and drive groundbreaking advancements.
Where it all began…
In the 1980s, Cebi was renowned as a market leader with its innovative tape deck mechanism, setting the standard in precision, reliability, and competitiveness. Faced with the technological shift due to digitalization, the technical team at Cebi began exploring new sectors and technologies. During this pivotal time, Cebi was forging stronger connections with renowned German automotive manufacturers.
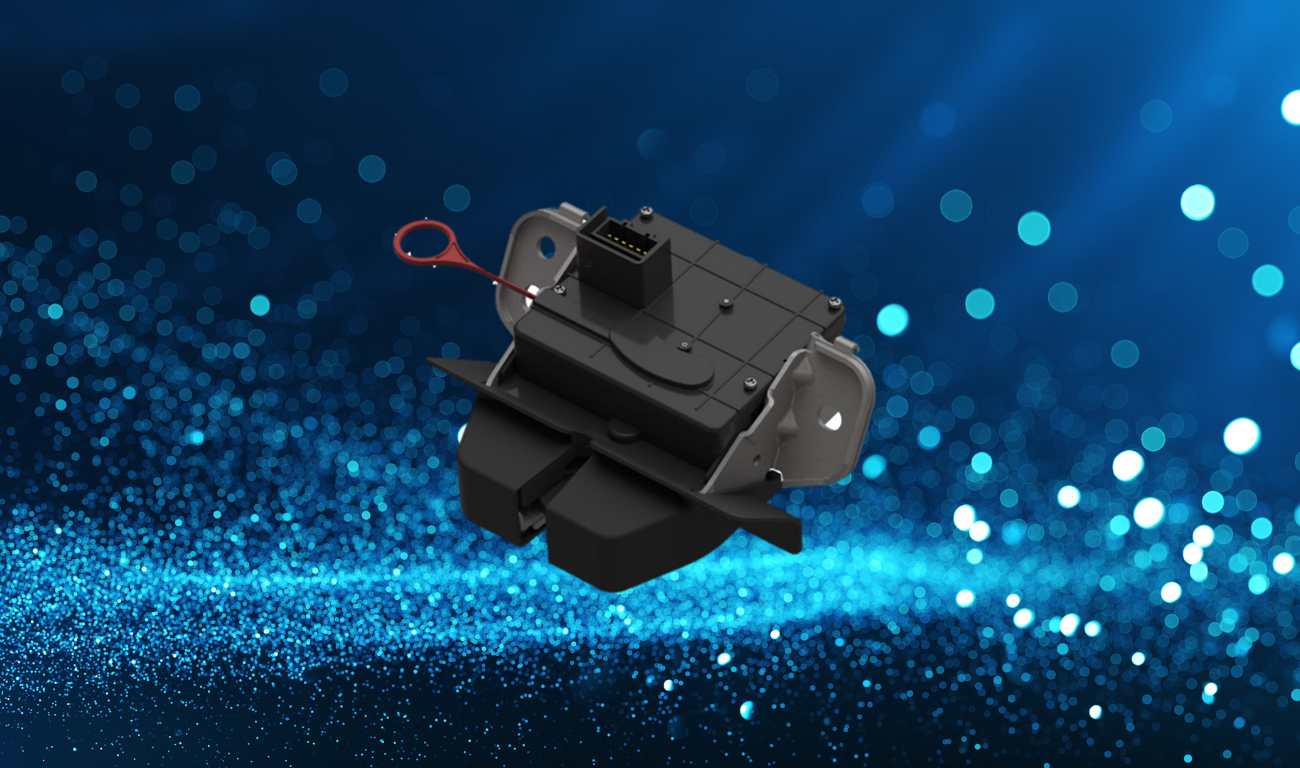
The automotive industry’s growing demand for sophisticated electromechanical components like closing systems presented a perfect match for Cebi’s capabilities. There was a search for a solution to make systems safer and more convenient from a functional point of view, but the existing solutions were rather makeshift and unreliable in all usage conditions.
First Challenge Solved
After three years of persistent effort, Cebi reached a turning point in 2003. During a crucial meeting with a German carmaker, Cebi reviewed an existing latch and identified unmet specifications in the existing latch, presenting a unique opportunity. With the expertise of Cebi's technical department, they proposed a solution that met all requirements and developed a prototype that was successfully tested. This achievement marked Cebi’s first nomination for the latch, eventually securing a significant production volume.
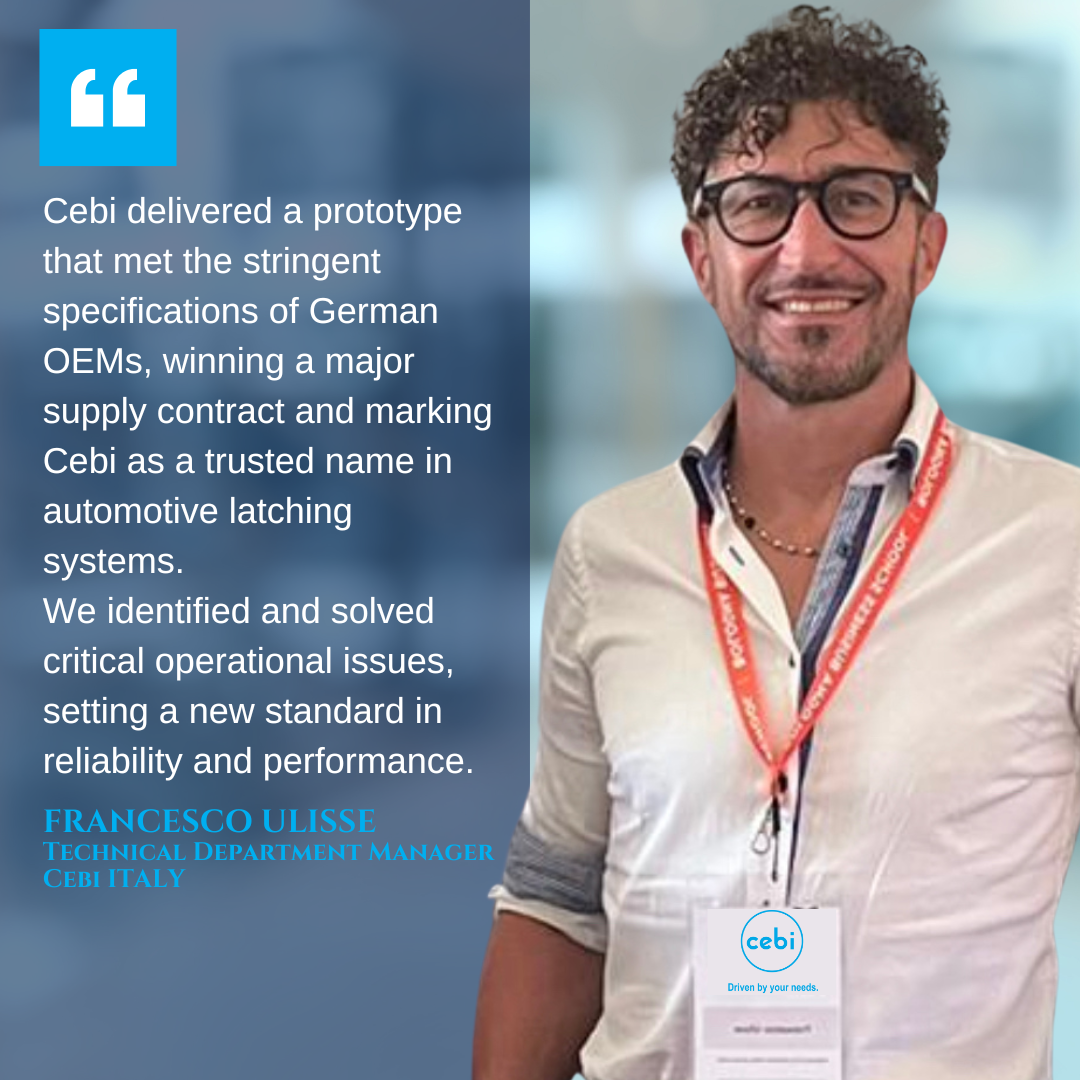
Through dedicated problem-solving, Cebi worked systematically to enhance the design: they ran extensive laboratory tests, identifying an issue in the opening phase, which led to concept analysis and a redesigned prototype.
Pioneering Actuator Technology
In 2010, a German carmaker sought a highly specialized actuator for the “tchin-tchin” latch, setting high specifications for closing force and reliability. Responding to this need, Cebi’s engineering team developed an innovative actuator with a unique mechanism: the actuator operated electrically during closing while allowing for mechanical operation during opening. The solution used a spiral spring inside the actuator and represented the first generation of Cebi’s patented actuators.
Tailgate Latches for rear doors, read windows for Trucks and cars
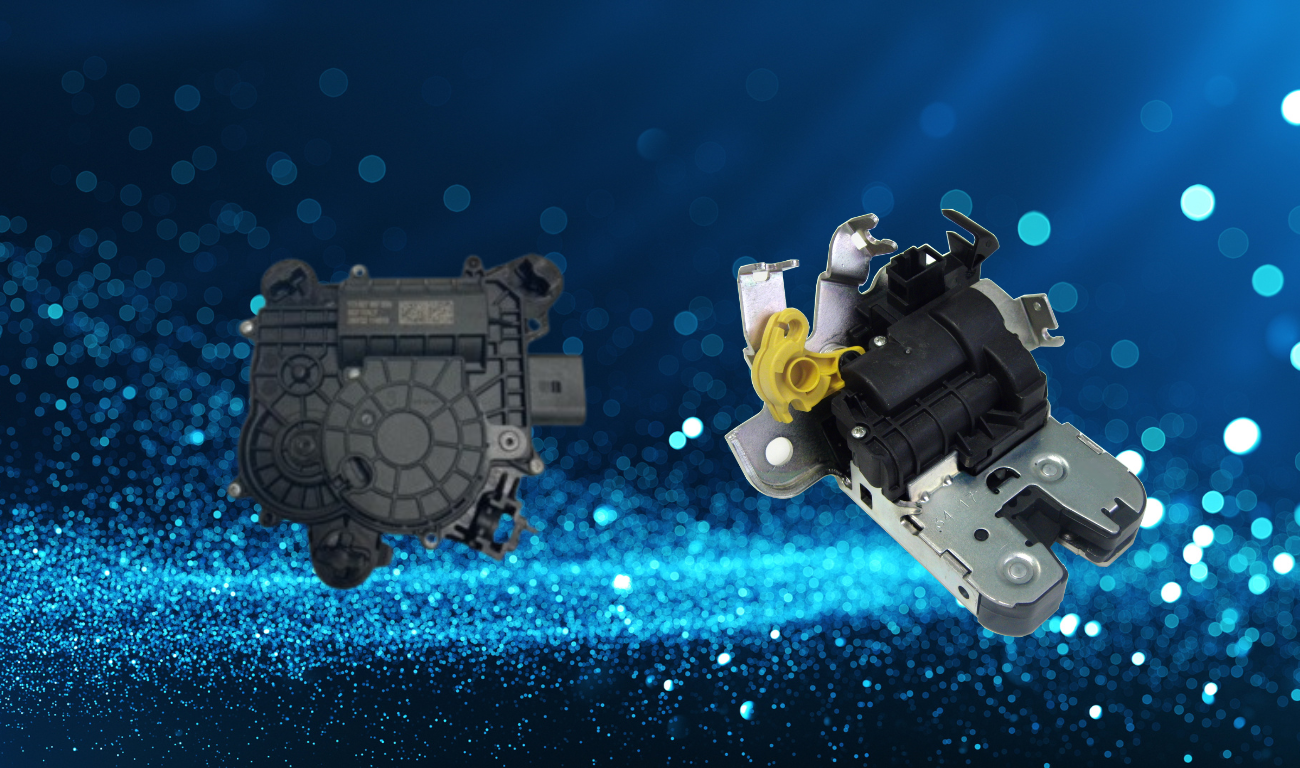
The second-generation actuator saw significant advancements. This version enabled both opening and closing functions to be fully electric, eliminating the need for mechanical operation. Cebi improved upon the initial design by reducing weight and noise—a key consideration for electric vehicles (EVs), where noise control is critical. Cebi’s engineers faced the challenge of minimizing motor noise, fine-tuning motor dimensions, torque, and gear design to achieve a quieter, more efficient actuator. Second challenge met with flying colors!
Optimized Time-to-Market
Since many years, Cebi has extensively built upon the use of advanced analytical tools to accelerate product development. For instance, using CETOL software, Cebi’s engineers analyze tolerance systems early in the design phase, allowing them to identify potential issues without needing physical prototypes. Finite Element Modeling (FEM) simulations further enable them to test and refine designs digitally, streamlining the process and reducing time to market.
These tools and Cebi’s meticulous approach have allowed for faster innovation cycles, making it possible to swiftly adapt to customer requirements and ensure top performance across all components.
Influencing industry standards
The transition from purely mechanical locks to electromechanical solutions was revolutionary, even though initially meeting scepticism from both OEMs and competitors. However, as Cebi’s latching system demonstrated unparalleled consistency in extreme conditions—from -40° to +80°C and across the entire voltage range—it soon became the benchmark, influencing industry standards and expectations.
Meeting OEM Demands with Modular and Scalable Solutions
In the competitive landscape of automotive components, Cebi stands out not only for its innovation but also for its ability to create modular, scalable designs that are highly automatable. This focus on modularity and automation enables Cebi to deliver on OEM demands for reliability, durability, and low noise levels.
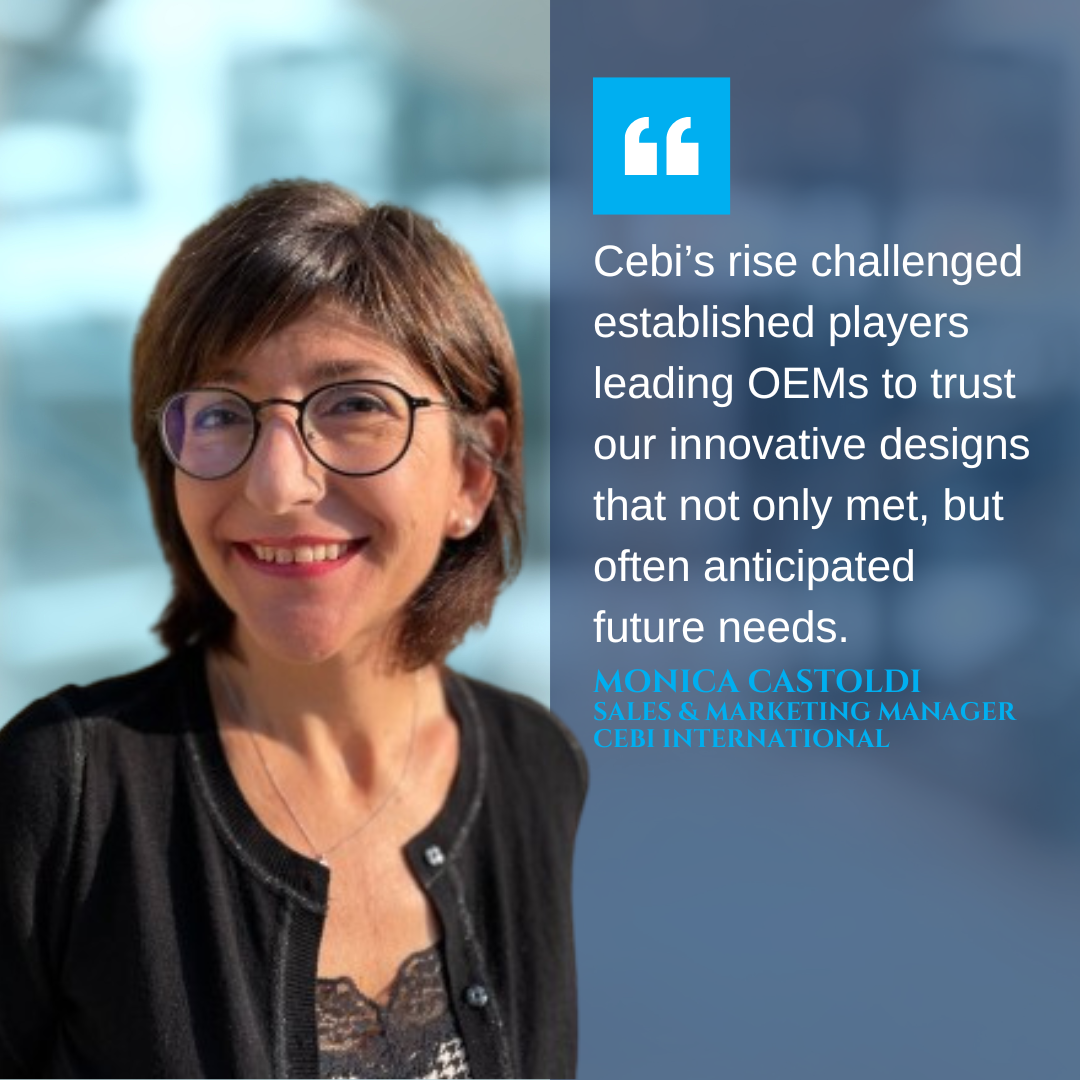
Cebi’s success lies in a philosophy of continuous improvement, which combines hands-on collaboration with OEMs and in-depth R&D exploration. The company’s diverse teams bring together experienced engineers and fresh talent, a blend that fuels creativity and drives solutions for the evolving demands of automotive latching systems.
With an eye on future trends, Cebi continues to proactively propose enhancements that align with emerging market needs, solidifying its role as a critical partner for automotive innovation.
Conclusion
Through its pioneering latching systems, Cebi has transformed from a respected market leader into an industry innovator, redefining what’s possible in automotive component technology.